New Defect Reporting Process
Identifying and addressing defects promptly is critical to maintaining the quality, safety, and reliability of operations across all projects and sites. The New Defect module enables users to systematically record, track, and resolve defects that arise in equipment, materials, systems, or processes. Proper documentation not only ensures timely rectification but also helps in preventing recurrence and improving overall operational standards.
Selecting Project and Defect Details
To initiate the defect reporting process, the user must first select the project name where the defect was observed. Accurate project selection ensures that the defect is linked to the correct site and enables appropriate tracking and follow-up actions.
Following this, users must choose the defect occurrence date and time, specifying when the defect was first identified. This distinction between occurrence supports accurate record-keeping and timely management.
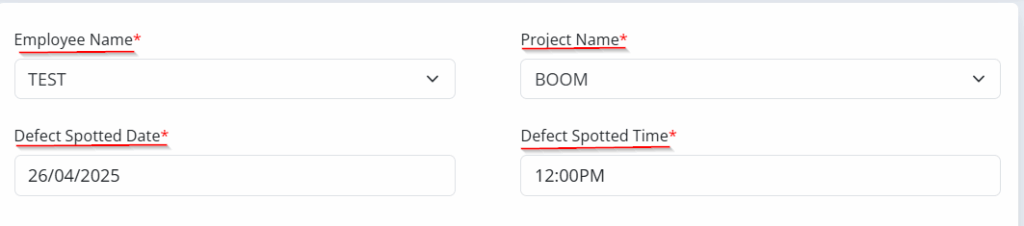
Identifying Defect Type and Severity
Next, users must select the type of defect from the available options. Types could include structural defects, equipment malfunctions, material deficiencies, workmanship issues, or system failures. Choosing the right type categorizes the defect correctly for technical and management teams.
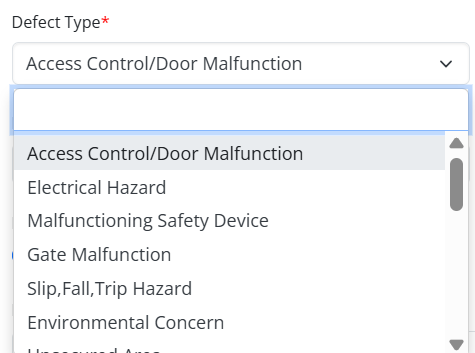
Recording the Defect Location and Status
It is essential to mention the exact location where the defect was detected. Detailed location information, such as the building, floor, equipment ID, or system area, helps in quick access and targeted rectification efforts.

The user must also define the defect status by selecting either Open or Closed:
- Open indicates that the defect is pending review, action, or resolution.
- Closed signifies that the defect has been addressed, verified, and no further action is required.
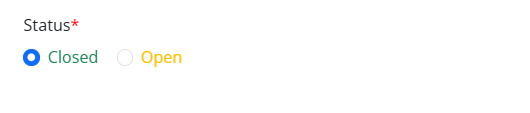
Describing the Defect
A comprehensive defect description is required to clearly explain the nature of the defect, how it was discovered, and any immediate observations. A good description should be factual, detailed, and objective, providing sufficient information for the investigation team to understand the full context.
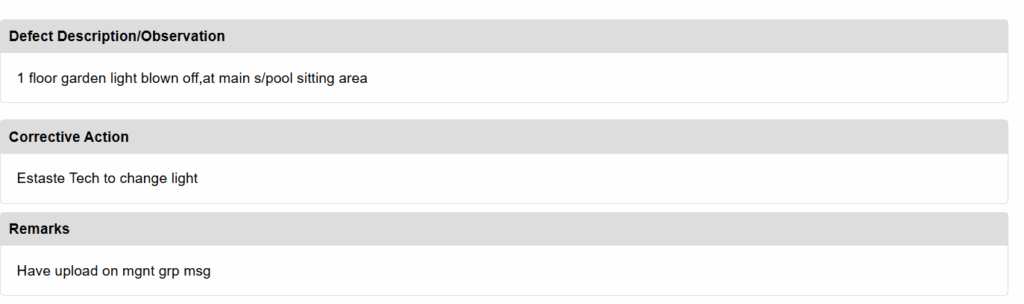
Users should also attach supporting photos or documents via the Add Attachment option. Visual documentation, such as photographs of cracks, damages, leaks, system errors, or any abnormalities, strengthens the defect record and aids in faster and more accurate diagnosis.
Documenting Actions Taken
Under the Action Taken section, users should record all measures implemented to manage, contain, or correct the defect. This may include temporary fixes, full repairs, equipment replacements, or operational adjustments. Thoroughly detailing the actions ensures that all stakeholders are aware of the resolution steps and facilitates audit trails.
Conclusion
The New Defect module provides a structured and efficient process for capturing all relevant information regarding defects. Proper use of this system supports faster resolution, enhances accountability, and drives a culture of quality and safety. By carefully documenting each step—from detection to closure—organizations can build stronger, more reliable operations and deliver better outcomes for all stakeholders